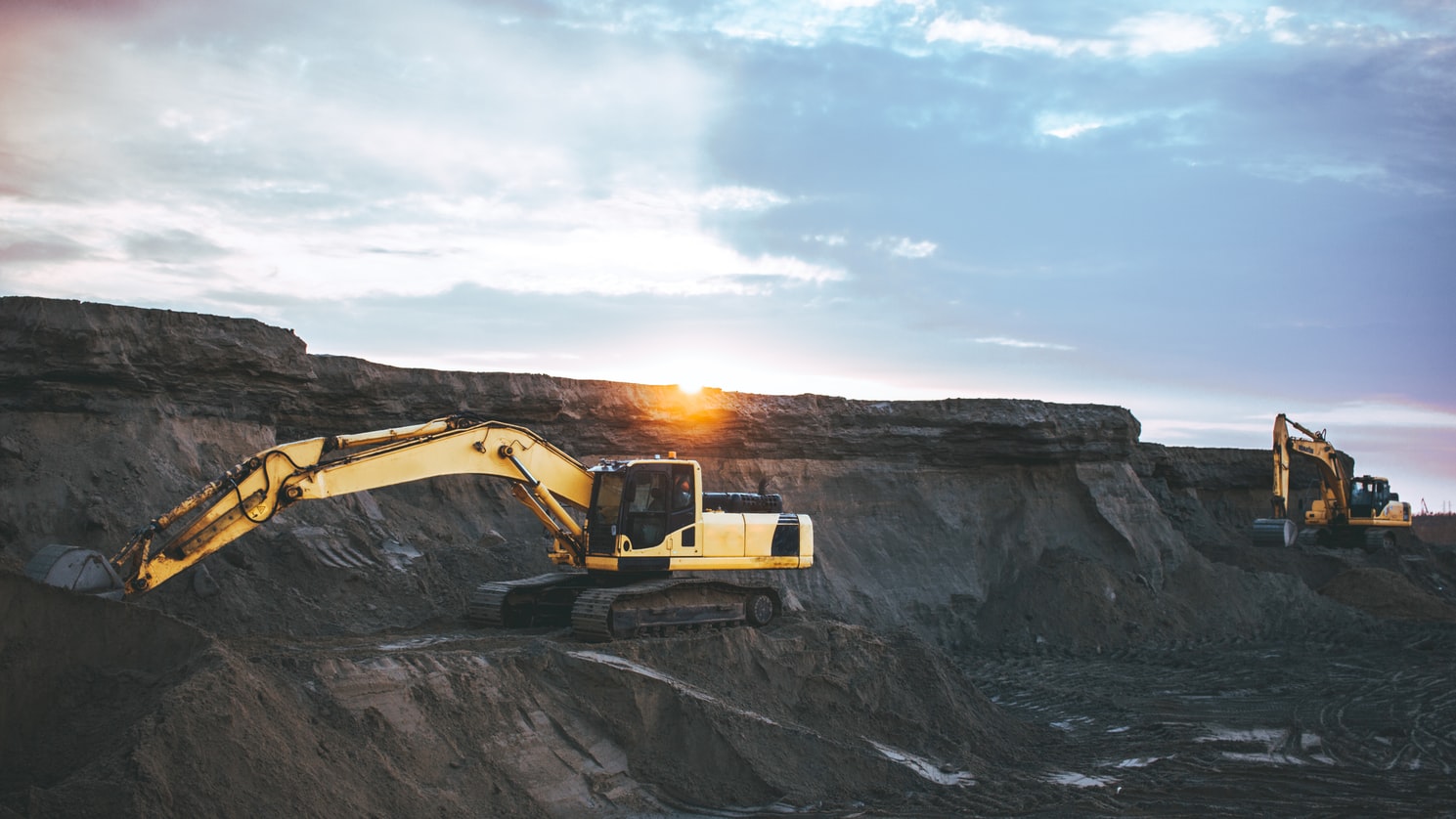
Context
A North American mining corporation, faced with unexplained losses on their balance sheet, sought to gain a new perspective on their manufacturing operations. They suspected that there were gaps in their knowledge of how operational downtime was impacting their revenues. Their traditional operational metrics, which examined each of their manufacturing processes separately, was not providing the needed insights. The company could only make estimates or guesses about the potential downtime impact. This was unacceptable. A new approach was needed.
Solution
The company reached out to the Arcurve team to get the answers they needed. The Arcurve Advanced Analytics team leveraged a ground-breaking data management, consolidation, integration, and contextualization service that is uniquely suited to close the knowledge gaps that often plague enterprises. To address this company’s needs, Arcurve used its custom tool-set to unify nine different real-time data sets associated the company’s mining processes and ranging from direct telemetry from mining machinery and continuously collected downtime analytics to daily mine output data and financial reports.
In a matter of days, the Arcurve team deployed its customized technology to connect the Company’s various data-generating processes to a Neo4j knowledge graph database. This was the first time the company had been able to combine all of its manufacturing and financial processes into a single useable knowledge resource. The Arcurve team partnered with the Company’s subject matter experts to develop new analyses of the patterns and relationships contained within and between all these data sets. Quickly, the analytical team was able to absolutely determine that previously unexplained losses were the direct result of equipment downtime. The scale of the losses was 300% greater than the company had previously estimated, elevating the downtime-related losses from something that had been considered a “cost of doing business” to something that was deemed to be mission critical. The business understandings generated by the Arcurve Advanced Analytics team helped the client make business-changing adjustments to their manufacturing process.