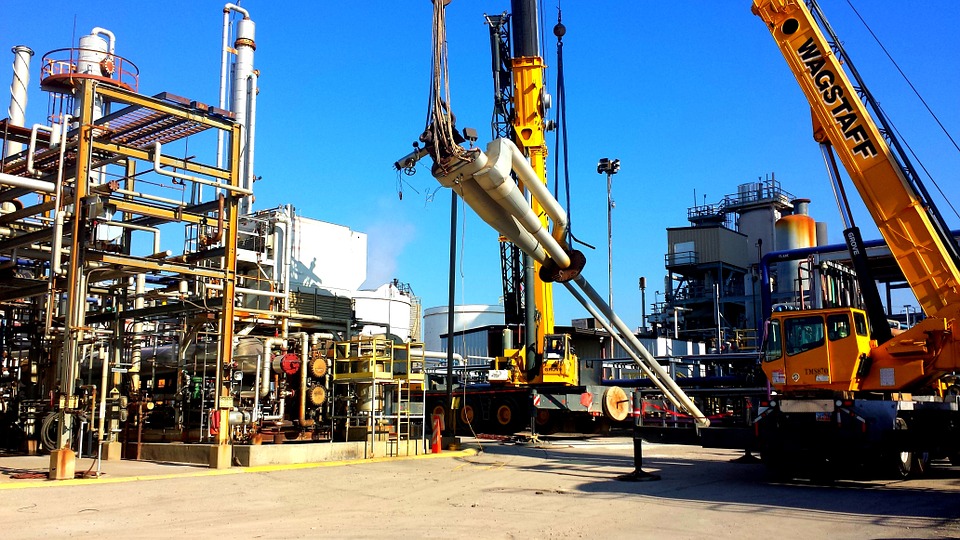
Context
The energy industry has come under enormous pressure to reduce costs in recent years. In response to this pressure, and to improve efficiency, our client is applying manufacturing-line automation to tasks that have traditionally been labour intensive. The equipment involved is industrial in scale, large and powerful and easily able to create situations hazardous to workers. A system of interlocks comprising mechanical, electrical, and process components with an accompanying mobile application had been developed by our client and a third-party software developer. The system mostly worked but suffered from data “glitches” as well as quality and configurability issues that caused concern for our client.
Solution
Arcurve reviewed the system as it existed and identified several opportunities for improving the robustness and feature set of the overall system. The way that data was edited and saved were not very robust, and the way that checklists were configured wasn’t as flexible as the client required. In collaboration with the client, Arcurve implemented the changes, both on the “back end” automation control system, and on the “front end” mobile application. In collaboration with the client, Arcurve thoroughly tested all changes to ensure the overall system performed as required.
Upon completion of the changes, the data glitches were no longer present, and the application had additional functionality that improved the overall usefulness of the system.